Equipment for heat pressing shoe parts


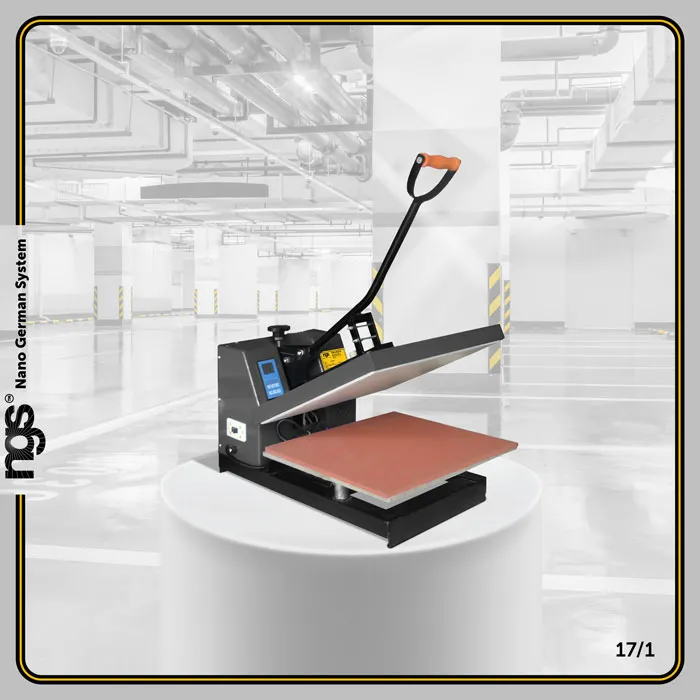
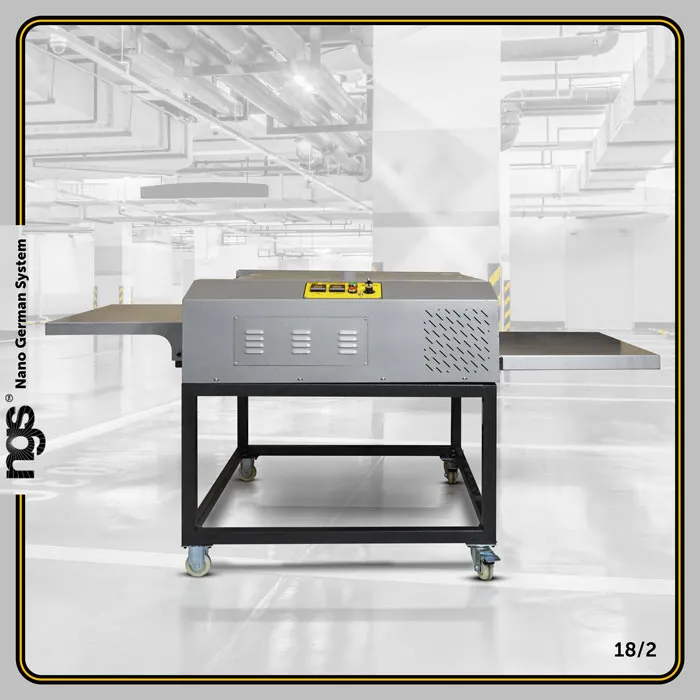
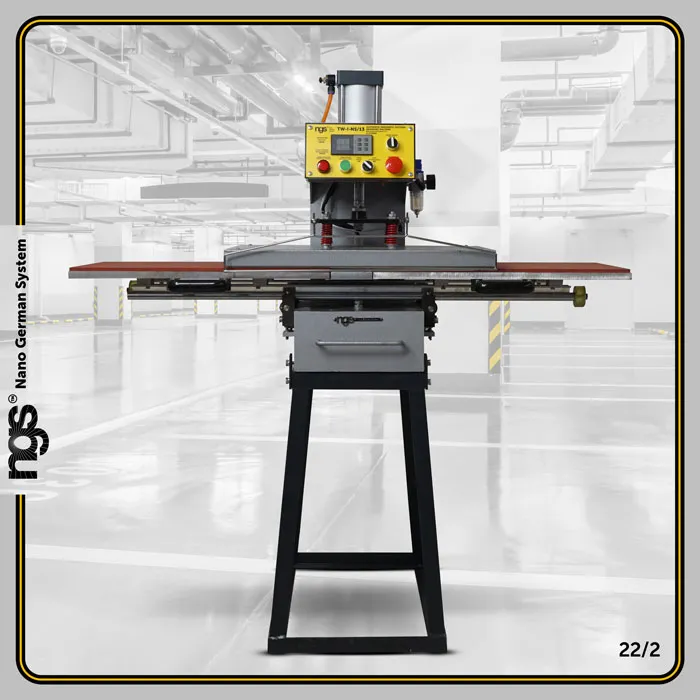
Equipment for hot pressing details of leather shoes is designed to turn unprocessed material into a workpiece suitable for sewing shoes. Typically, in shoe production, double-presses glue inter-lining materials with the upper of the shoe under high temperature by a clamping method. The wide surface of the working area of the press allows you to simultaneously process several parts at once, thus distributing the pressing force equally between them, which helps to prevent delamination of the processed materials.
High-quality duplicating machines are equipped with electronic time control functions, controllers and temperature indicators, as well as an audible and visual signal to complete the heat pressing process.
For hot press equipment, the availability of manual and automatic modes with the ability to switch between them is the norm. In manual mode, the gluing cycle is started by simply pressing a button, in automatic mode, when the table reaches one of the set end positions. Such maneuverability in the production cycle cannot but affect the flexibility of the production process and improved productivity as a positive factor. Also, reducing the load on some sites and transferring production resources to others allows optimization and saving time and financial resources.In the production of shoes and leather goods, it is impossible to do without hot press equipment, if only for the reason that there is a constant need to hot press not only the upper materials of the shoes, but also leather with leather, fur and just fabric in other areas of leather goods manufacturing.
A high-quality heat press should have a stable heating power and a sufficient indicator of the maximum temperature for heating the working surface. This all directly affects the performance of the heat pressing machine, and this is the most important indicator, which is measured in the number of cycles per eight-hour shift. Good productivity, which can ensure stable growth and retention of production rates, is about 700 cycles per shift. Moreover, the larger the area of the work surface, the more parts can be placed on it and processed.
More...
Ask a Question