Shoe manufacturing equipment


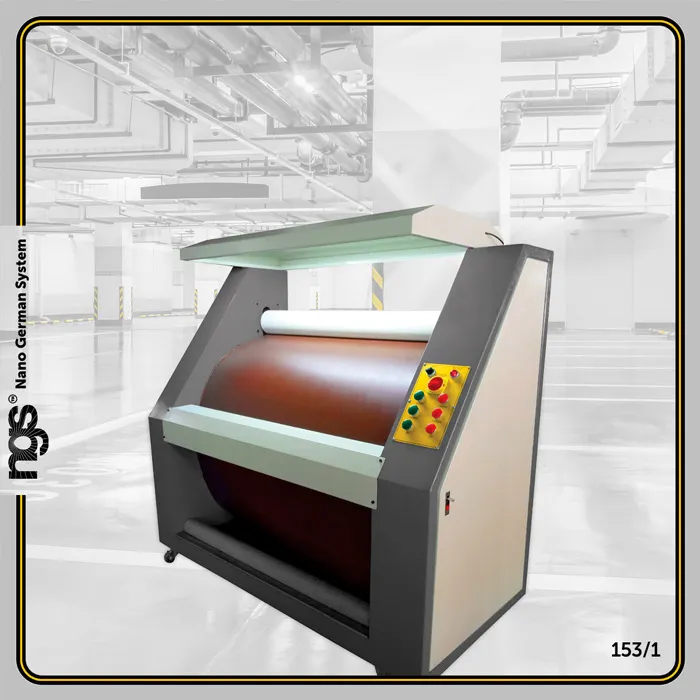
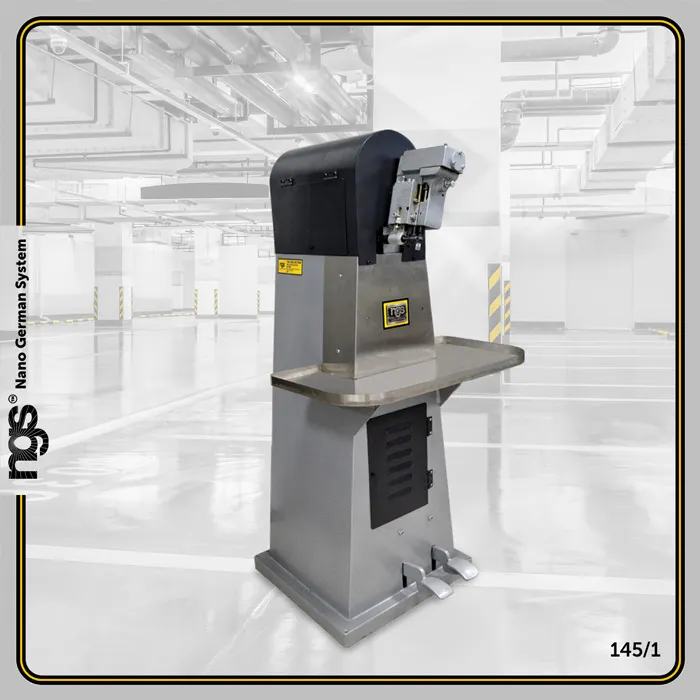
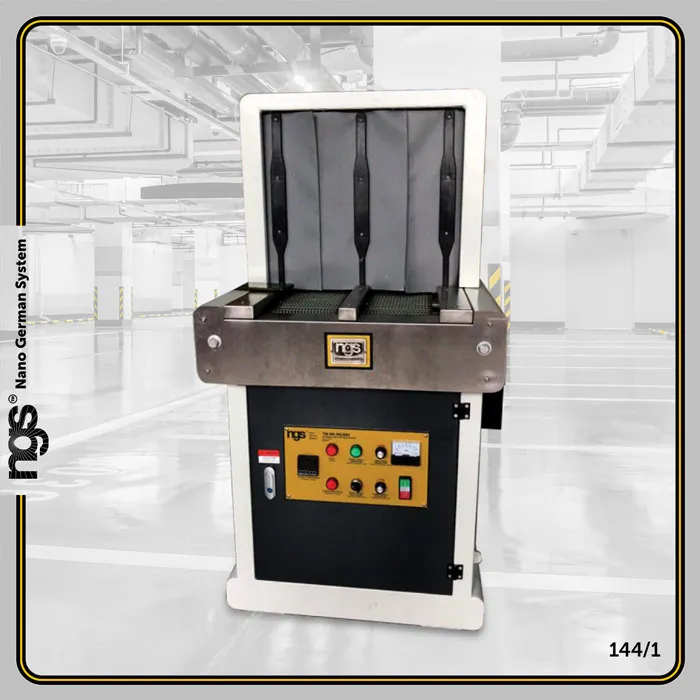
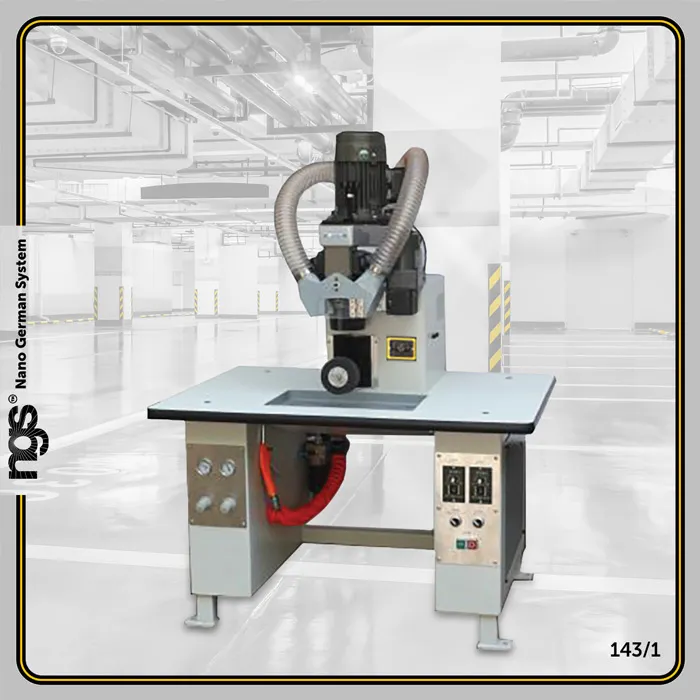
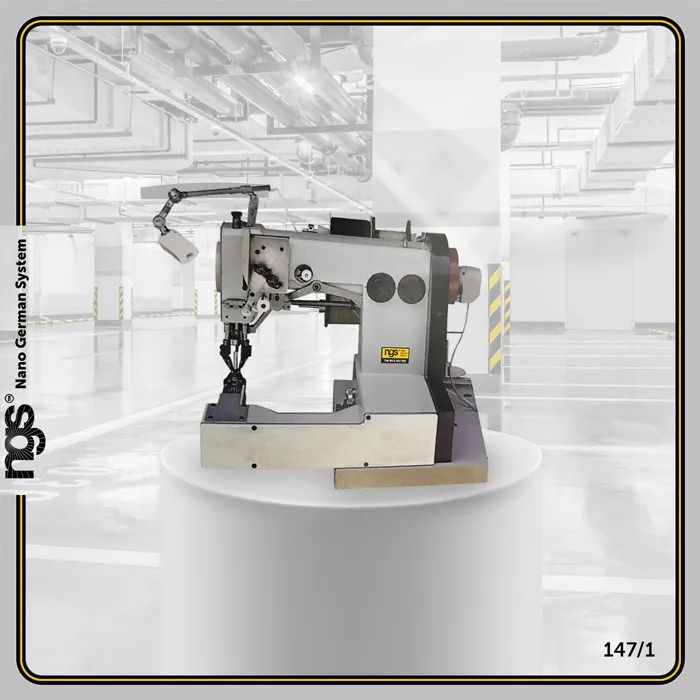
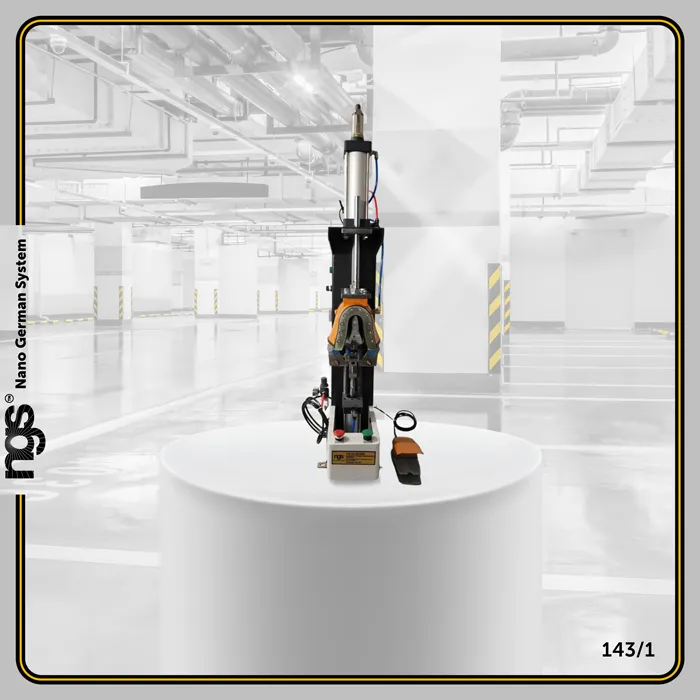
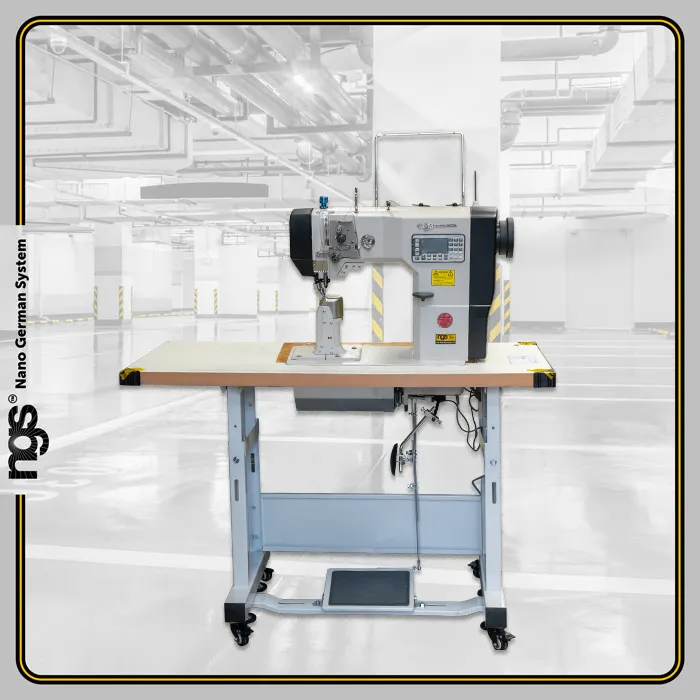
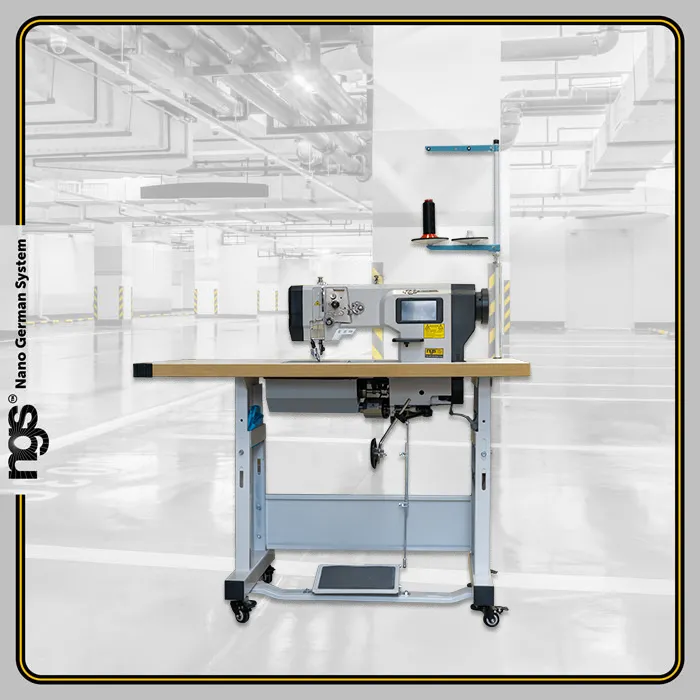
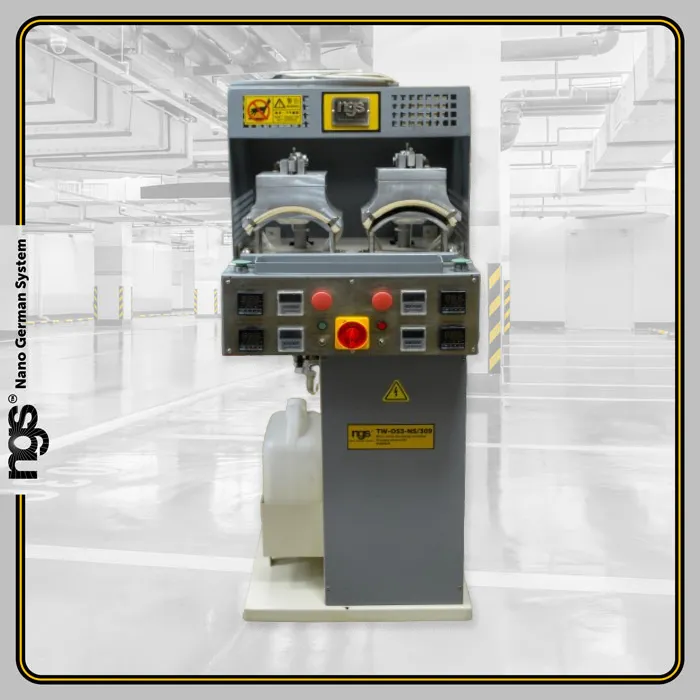
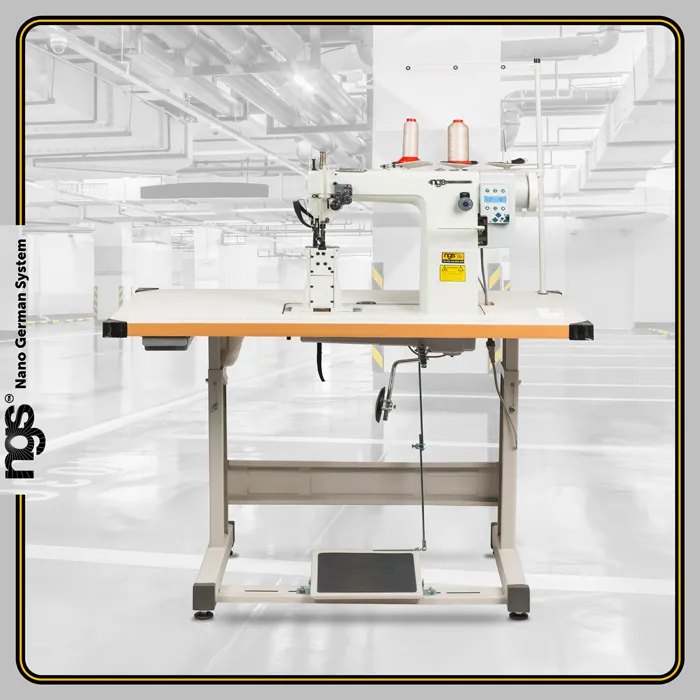
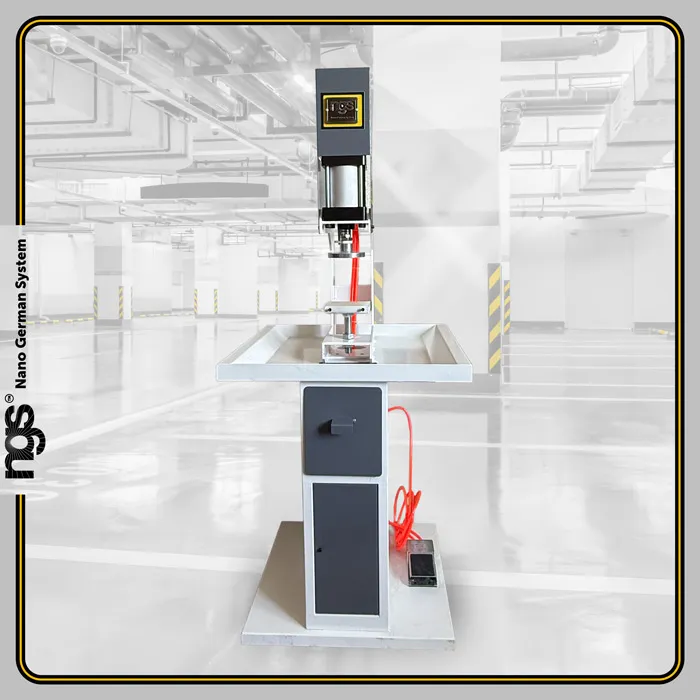
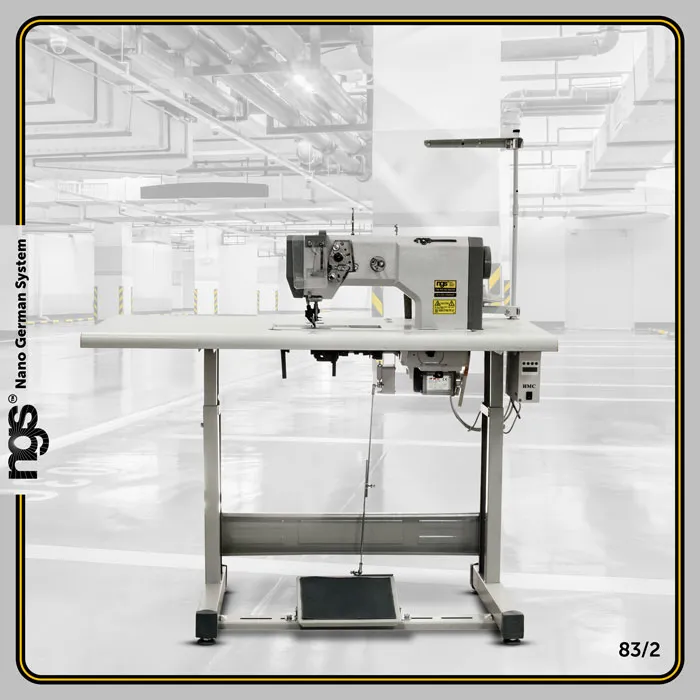
The international company NGS offers the widest range of equipment for assembling completed lines for different stages of shoe production. In general, there are four main stages:
- cutting section;
- assembly of the workpiece;
- lasting shoes;
- finish area.
In the first part of the cutting section, it all starts with a measuring machine (horizontal or vertical), designed specifically for measuring finished leather, which can also be equipped with automatic printing or stamping functions on the back of the skin. The hydraulic cutting press with the setting of cutting points, as well as the dividing machine for separating soft and hard leather, which has the functions of steplessly adjusting the feed rate and automatic tool grinding, are integral parts of the cutting section, which provide not only high productivity, but also high quality products. The cutting section also includes presses for the installation of accessories and a machine for automatic filling of pearls.
The second part of the cutting section is represented by a skiving machine, which is suitable for working with any kind of surfaces in the manufacture of shoes, bags, belts, wallets and other accessories. Also on this site are presses for applying cliches (also designed for surface stamping), numbering machines (clear and precise stamping of serial numbers, sizes and dates) and duplicating machines, which are responsible for gluing the backing pad with the material of the upper of the shoe under the temperature, pressing method . Duplicating machines are additionally equipped with time monitoring functionality, temperature sensors and process completion indicators.
At the first installation site, in other words, at the assembly site of the workpiece are presented:
- pneumatic or hydraulic exhaust machine with settings for pressure, speed, time and temperature, with hot and cold molding;
- a machine for bending the edges of leather and forming a vamp;
- a flat machine for assembling the lining with a zigzag stitch;
- single-needle core machine or two-needle sewing machine (there are models equipped with a computer), which is used for sewing shoes, bags and leather goods of the highest quality;
- a machine for flattening and smoothing the seam, equipped with a percussion mechanism that loosens the seam and smoothes leather and makes it more elastic;
- a machine for applying glue to a zipper with a pre-installed pawl (suitable for making shoes, bags and wallets);
- equipment for sealing and dyeing the edges of leather, designed to apply paint to the edges of leather and then dry them. The drying chamber is equipped with infrared lamps that heat the air and electric fans to ensure air circulation;
- The insole stitching machine is usually used to sew sports or children's shoes, but can also be used for sewing waterproof clothing, work gloves, medium-thick fur, and other materials.
The second assembly section, on which the sewing itself and the shoe lasting itself, are usually equipped with the following equipment:
- machine for pasting a toe with a triac control of the heating temperature;
- a table for applying latex glue to the lining of the upper shoe and subsequent bonding of the upper and lining (it must be equipped with a hood);
- machine for gluing the lining;
- Equipment for molding the heel of shoes with direct cooling, air cushions and a laser sight for perfectly accurate placement. This machine must necessarily have the ability to adjust the temperature, time and tension of the workpiece;
- a machine for steaming the heel with digital adjustment of the heating temperature of the workpiece and the amount of steam supplied;
- machine for moulding vamps;
- machine for steaming vamps with setting the time and amount of steam supply;
- machines for the glue lasting of the toe from the ZNK series and of the middle with the heel from the ZPK series;
- a machine for trimming and smoothing the lasting edge in the toepart;
- automatic installations for heating;
- an air dryer with a nibble, which should be equipped with a roller for rolling and have the function of adjusting the intensity of the steam with the possibility of turning it off for heating only with hot air;
- a machine for molding the backpart for the heel - if it is possible to adjust the temperature of the pressure plate, quickly adjust to the style of the last and control the degree of heel lapping, it allows you to form a perfect fit in the lapis part of the heel;
- a machine for marking the soles before ruffling the workpiece and applying glue. Using this machine, you can ensure an extremely accurate line of roughing and glue the workpiece to the sole with an accuracy of millimeters;
- a machine for coarse roughening the workpiece and leveling the footprint with an abrasive stone (must be equipped with a dust collector for waste);
- glue activation machine;
- hydraulic or pneumatic press for gluing soles;
- a machine for nailing a heel with a laser aim and adjusting the force and position of the hammer. It is also highly desirable that the functionality includes the ability to adjust the supply of nails (automatic or manual) and nailing (simultaneous, alternating and other more subtle settings in the menu);
- chiller with the functions of quick freezing and automatic defrosting (these aspects will help save energy and production time);
- a machine for removing shoes from lasts, equipped with the ability to adjust the angle of rotation;
- a machine for sewing the sole with speed adjustment functionality and the ability to directly intervene in the programmed operation of the computer. Suitable for sewing the soles of moccasins, sports shoes and casual shoes.
And finally, the final stage of shoe production is the final processing. For this process are used:
- machine for molding counters;
- machine for applying glue to the insole;
- single or double rule for shafts with an airdryer designed to shape the shafts of boots. An air dryer with a steam supply function allows you to quickly remove wrinkles from the leather and smooth it out as much as possible;
- spray booth in the ability to wash off excess paint using a water system built into the machine. Be sure to have a hood for harmful fumes in the paint compartment;
- polishing machine with a modern converter, which is equipped with functions of step-by-step speed adjustment. The machine should also be equipped with a dust collector with a filter made of a thin nylon mesh, to which dust does not stick and which is very easy to clean from contamination due to its high breathability;
- various vacuum cleaners and washing machines necessary to remove dirt in hard-to-reach places.
All the equipment presented above is for understaffing production lines or for creating them from scratch.
More...
Ask a Question